Double-Sided Flat-Honing Holds ±2μ, Speeds Production
A new fixed abrasive flat-honing technology has expanded the materials and tolerance capabilities of a shop specializing in precision lapping.
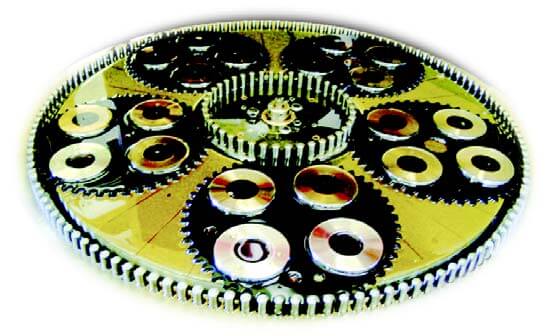
Using the Stahli DLM700, ProLap is able to produce parts with tolerances of ±0.00008″ (± 2μ) and 2 – 4 Ra surface finishes.
ProLap – Production Lapping Company, Inc (Monrovia, CA) opened its doors in 1961. ProLap’s focus was on contract lapping and machining for a variety of customers. Some include aerospace, medical, semiconductor, undersea exploration, space exploration, mechanical seal, and other commercial industries. “Our strategy right from the outset,” says Steve Herzig, president of ProLap, was to deploy the latest machine technology. Maintaining a competitive edge, while delivering close tolerance components to our customers.”
Consequently, A new precision honing machine from Stahli USA (Wauconda, IL) is allowing the company to do just that. Expanding its material processing capabilities speeding up production.
ProLap is equipped with the most state of the art lapping and free abrasive machining systems. In return, it allows them to take on virtually any flat surfacing application. Single and double-sided lapping and polishing capacities can include parts as small as 0.125″ in diameter. And can hold parts as large as 60″ in diameter, to parts as thin as 0.002″.
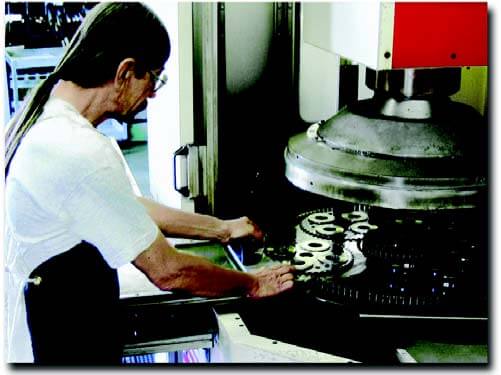
Flat-Lap’s Specialty Process
Herzig points out that ProLap has always been a leader in flat-lapping technologies. “We were the first job shop in the U.S. with double side lapping capabilities,” he notes. “The applications for lapping vary from the ultra-precision. What most people think of when they think of lapping, to first surfacing on a casting, to high stock removal. Flat-lapping can replace a grinding, milling, or a turning operation. All of this can be easily done with little or no stress being introduced into the part.”
Herzig was aware of the concept of fine grinding or flat-honing for many years.
Herzig always was envisioning that someday this type of technology could be included at ProLap. Two years ago, Herzig was in contact with Stahli USA, manufacturers of single and double-side flat-honing precision machines. Stahli has pioneered the concept of flat honing and has continually refined this technology. Herzig notes that when he first heard there was a new machine on the market. “we jumped on it without really having any work for this machine. I just knew this was the next logical progression in the evolution of lapping/grinding and we had to be part of it.”
New Machine Technology
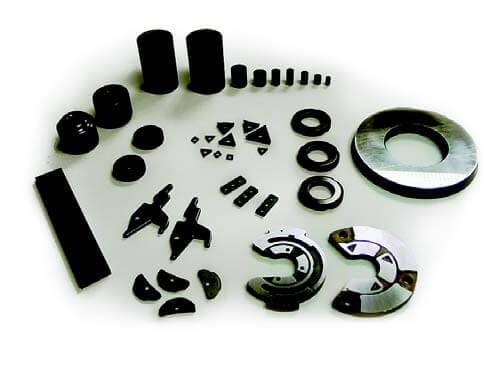
In 2003 ProLap took delivery of a Stahli DLM 700. This model is a double-sided flat-honing machine that features a unique dual wheel design. This enables both sides of flat pieces to be complete simultaneously. The uniqueness of the Stahli flat honing process is; inquiring the same or greater precision finish by using fixed abrasive compared to loose compound or slurry associated with conventional flat lapping. The Stahli DLM 700 operates using bonded CBN or diamond particle wheels.
Herzig notes that the impact of the Stahli has been across several different fine grinding applications of varying materials and tolerances. One of the most dramatic process improvements realized by ProLap after the installation of the Stahli was with a hardened (65 Rc) steel blade they manufacture for a customer in the medical industry.
The blade requires very close tolerance +/- 0.00005″. Prior to installing the Stahli, the process involved loading 40 of these parts into one of ProLap’s larger double-sided lapping machines. The entire process would take approximately 4 hours from start to finish, which included cycle time for lapping, inspection, cleaning, and packaging. “With the Stahli”, he continues, “we can process 20 parts in about 20 minutes. We still lap the parts to maintain the same surface finish/appearance even though the Stahli can more than hold the tolerance.”
The process continues..
One of our more difficult projects for ProLap is the grinding of the end faces of ceramic roller bearings. The length versus diameter of these parts is what makes them particularly difficult to process. These parts vary in dimension from 5mm x 10mm to 32mm x 52mm. In addition, stock removal required 0.030″ – 0.050″ (0.76 – 1.27mm) of material; while holding an overall length tolerance of ±0.00008″ (± 2μ) and a surface finish of 8 Ra or better. When the project started initially the parts were being ground and then lapped and polished in multiple operations.
ProLap engineers determined that processing time on this part could also be improved by running them on the DLM 700. In just a single set-up and operation, the DLM 700 has been able to meet this requirement and actually exceed some of the requirements. ProLap is experiencing a consistent surface finish of 4 Ra or better.
Precision of speeding up production
Another grinding challenge Herzig mentions is maintaining consistent flatness in grinding ceramic inserts for several manufactures. The smallest of these inserts are approximately 0.200 sq.-in. and range up to approximately 3″ in diameter. Herzig also notes that before sending these inserts to ProLap, many of their customers were already grinding these parts in-house. Although, they were using a traditional single-side grinder that required machining one side, then the next. A time-consuming process, to begin with. Often after the parts were inspected, these parts would need yet another operation to maintain parallelism and flatness. With the Stahli, ProLap is able to process both sides at once while holding ±0.0001″ and a 2 – 4 Ra surface finish.
Future Plans
With each new job that’s run on the DLM 700,. ProLap is discovering additional opportunities that extend their process capabilities. In addition to steel and ceramics, ProLap has expanded precision fine grinding to include other materials; such as powdered metal parts, as well as many different ceramic materials including alumina, zirconia, silicon carbide, silicon nitride, and various grades of carbide. “We are currently investigating either purchasing or adapting the fixed abrasive technology to some of our single-side lapping projects,” concludes Herzig. “What we have experienced in improved cycle time and product finishes are great for us and our customers.” Stahli USA